Your cart is currently empty!
Process Manufacturing
The process manufacturing industry produces goods by combining raw materials, supplies, or ingredients following specific formulas. This sector encompasses industries such as chemicals, pharmaceuticals, food and beverages. It relies on continuous production (24×7) processes and places a strong emphasis on quality control and regulatory compliance to ensure product consistency and safety. A significant challenge currently facing the industry is the need to adapt to increasing regulatory demands and sustainability pressures while maintaining efficiency and reducing operational costs.
Benchmark Six Sigma offers problem-solving approaches that can greatly assist organizations within this industry in enhancing quality and operational efficiency. By employing methodologies like DMAIC (Define, Measure, Analyze, Improve, Control), companies can identify and eliminate defects, streamline processes, and optimize resource utilization. Benchmark Six Sigma provides data-driven strategies and best practices, enabling organizations to reduce variability, improve product quality, and achieve higher customer satisfaction. This systematic approach promotes a culture of continuous improvement, which is crucial for staying competitive in the ever-evolving landscape of the process manufacturing industry.
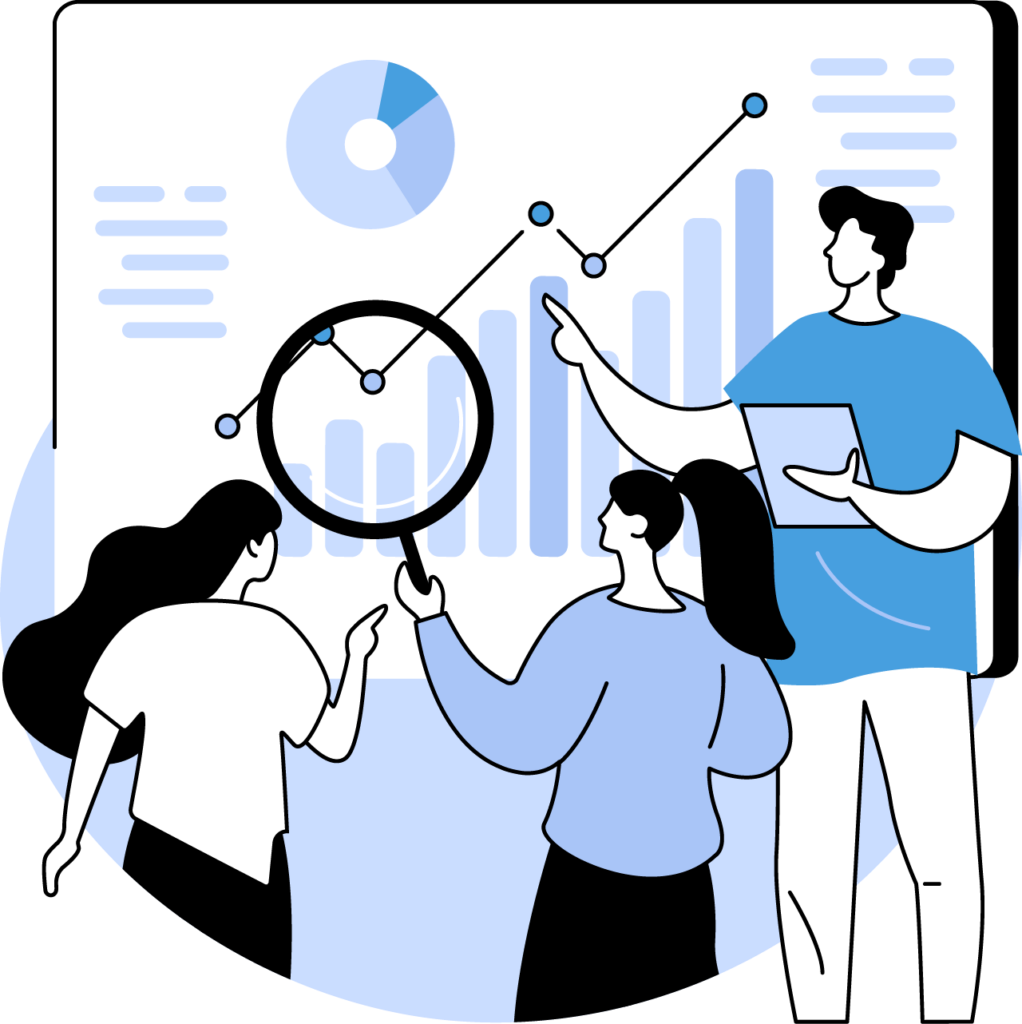
Caselets
Standardizing Measurement Accuracy
A Measurement System Analysis study was conducted at a starch manufacturing company as a part of the project to reduce the variation in starch moisture content. One of the causes identified was lack of standardization in the use of the moisture meter and hence the study was performed. A crossed Gage R&R design was used in the study. Key improvements involved installing a vibration stabilizer table for the moisture meter, revision to the SOPs, training of the floor staff by the lab technician on how the sample has to be collected and spread on the dish. With the improved calibration within the team, the measurements were more accurate and correction of the measurement system reduced the range of moisture content from 4.6%-17.4% to 7.1% – 15.3%.
Aligning Projects with Strategic Goals
The PMO identified a challenge in aligning its project portfolio with organizational strategic goals, leading to inefficiencies, resource wastage, and suboptimal ROI. To address these, the project team implemented Hoshin Kanri principles, developing a prioritization framework that evaluated projects based on ROI, strategic alignment, risk, and feasibility. A governance structure was introduced for continuous portfolio evaluation, along with optimized resource allocation plans. The project delivered significant benefits, including a 20% increase in ROI and a 15% reduction in resource wastage. By aligning 90% of projects with strategic goals, it minimized redundant initiatives and enhanced overall organizational performance. The optimized portfolio delivered sustainable value while improving stakeholder satisfaction and achieving long-term business objectives.
Enhancing Forecasting with Business Modelling
In one of the projects, issues with inaccurate sales forecasts, resulting in inventory shortages and excesses were identified that were costing the company INR 8 lacs monthly. To address this, the project team thought about using business modelling approaches to analyze the historical sales data using multiple regression techniques, identifying key factors such as seasonality, marketing expenditures, and economic indicators. The team developed a robust predictive model that enhanced forecasting accuracy by 25%. This improvement enabled more precise inventory management, reducing stockouts and overstock situations by 30%. Consequently, the project saved the company approximately INR 12 lacs annually and provided better predictions and forecasting for strategic decision-making.
Integrating TPM for Workplace Efficiency
The maintenance department of a conveyor belt manufacturer struggled with cluttered workspaces, inefficient tool management, and frequent safety incidents, which hindered productivity and increased accident risks. To tackle these issues, a project was done to implement 5S methodology (Sort, Set in order, Shine, Standardize, Sustain). This involved decluttering and removing unnecessary items, organizing tools and materials systematically, establishing regular cleaning routines, standardizing maintenance procedures, conducting continuous training for staff and regular audits. As a result, tool retrieval time was reduced by 25%, saving approximately 300 man-hours annually. Additionally, workplace accidents decreased by 40%, enhancing overall safety.
Reducing Defects with Lean Six Sigma
The Master Black Belt led a Lean Six Sigma project to reduce defects in the manufacturing line. The team identified excessive waste and variability as primary issues, resulting in a 15% defect rate. By implementing standardized work procedures and waste elimination techniques, they reduced defects to 5%. This improvement enhanced product quality and increased customer satisfaction. The project saved the company approximately INR 10 lacs annually by minimizing rework and scrap costs.
Implementing ISO-Based QMS
The project was done in a rubber valve manufacturing unit. The unit lacked a cohesive Quality Management System (QMS), leading to inconsistent quality standards and rejections from customers. The team developed and implemented a comprehensive QMS based on ISO 9001 standards, including documentation, standard operating procedures, and regular audits. Training sessions were conducted for all employees to ensure compliance. This integration enhanced overall quality consistency, decreased customer complaints by 40%, and increased client satisfaction, contributing to an annual INR 3โฏlacs revenue boost.
Streamlining Product Lifecycle Management
This Product Lifecycle Management project sought to streamline the lifecycle of a popular kitchen appliance plagued by extended time-to-market and high operational costs. The team optimized each lifecycle stage, from design to end-of-life, reducing time-to-market by 20% and operational costs by 10%. Team also implemented a new PLM software system. This efficiency translated to annual savings of INR 4 lacs and accelerated product launches. Additionally, integrating sustainability metrics improved the productโs environmental footprint, enhancing brand reputation.
Optimizing Strategic Sourcing
A strategic sourcing project was done for a starch manufacturing company. The company had a very large supplier base for corn and it was largely convenience sourcing leading to suboptimal quality of corn resulting in operational issues and lesser yield. The project involved defining key performance indicators such as quality, delivery reliability, cost competitiveness, accessibility and responsiveness. A standardized scorecard template was created, and performance data was collected and evaluated. Suppliers were informed about the new evaluation process and collaborated in setting realistic performance targets. As a result, the company improved the raw material quality, supplier delivery reliability and were able to make more informed strategic sourcing decisions. The project also enhanced risk management by identifying underperforming suppliers early, better controlled process leading to a yield improvement of 6% and strengthened the company’s competitive position through a more efficient and responsive supply chain.
Optimizing Water Usage for Sustainability
A sustainability improvement project was done in a beverage plant focused on Water Usage Optimization. The plant faced excessive water consumption and high utility costs, impacting sustainability efforts. To address these issues, project team implemented advanced water recycling systems and installed sensor-based monitoring to track usage in real-time. Additionally, they optimized cleaning-in-place (CIP) processes and upgraded to water-efficient machinery. These solutions enabled the reuse of up to 60% of water, significantly reducing fresh water intake. The project resulted in annual savings of INR 2.5 lacs in water and utility costs. Benefits also included enhanced sustainability through reduced environmental impact, improved compliance with water regulations, and a strengthened corporate reputation for responsible resource management. Furthermore, operational efficiency was boosted, supporting long-term profitability and environmental stewardship.
Driving Cost Savings Through Value Engineering
A Value Engineering project was done to reduce production costs of a household appliance without compromising quality. Initially, production costs were INR 10 lacs per batch. The team conducted a value analysis with a cross functional team and external SMEs, identifying alternative materials and optimizing manufacturing processes. They collaborated with suppliers to negotiate better rates, reducing costs by 15% to INR 8.5 lacs per batch. This cost saving of INR 1.5 lakhs per batch enhanced profitability and allowed competitive pricing, increasing market share by 10%.
Improving Sampling Techniques for Quality
An automotive OEM was facing the problem of frequent customer complaints and rejections even when the batches were internally inspected. The issue identified was the use of convenience sampling technique leading to a biased and very small sample size. A project was undertaken to statistically determine the correct sample size and identify the best sampling technique based on the nature of the processes. SOPs were updated and staff was trained to ensure sustenance of the project. The project resulted in 70% less customer complaints and 65% less customer rejections.
Benchmarking Compensation for Retention
An HR analytics project was carried out to do a benchmarking study for the Compensation and Benefit program. The organization faced challenges with retaining top talent due to non-competitive compensation and benefits, resulting in a high turnover rate of 18% at Senior Manager and above level and increased recruitment costs of INR 54 lacs annually. The team benchmarked salaries and benefits against industry standards, implemented equitable pay structures, and enhanced the benefits package by adding performance-based incentives, ESOPs and flexible work options. Additionally, the team introduced transparent communication strategies to ensure employees understood their compensation benefits. As a result, the compensation packages became industry-aligned, reducing turnover to 10% and improving employee satisfaction scores by 20%. This alignment not only enhanced employee retention but also positioned the company as a competitive employer in the market.
IoT-Driven Predictive Maintenance
An Internet of Things (IoT) project was done in a manufacturing division that faced frequent machine downtimes, costing approximately INR 50 lacs annually. To address this, the project team implemented a Predictive Maintenance System using IoT sensors on critical machinery. These sensors monitored real-time performance metrics and alerted the maintenance team of potential failures. The solution included integrating IoT platforms with existing ERP systems. As a result, unplanned downtimes reduced by 40%, saving โน30 lacs annually and enhancing overall production efficiency. Additionally, the data collected enabled better resource planning and extended machinery lifespan.
Optimizing Inventory Management
An inventory reduction project was executed at a leather products manufacturing company to reduce the cost associated with the raw material inventory. The project included studying the produce demand, variations due to seasonality, negotiations with the suppliers for time and cost, consolidation of suppliers for a tighter and integrated value chain and Just-In-Time principle. As a result of the project the raw material inventory value was reduced by 45% from INR 10,00,000 to INR 5,50,000. This initiative freed up capital, improved efficiency, and maintained customer service levels without increasing the stockouts.
Aligning Strategy with Hoshin Kanri
Hoshin Kanri workshops are conducted along with the senior management teams where the team aligns the companyโs strategic objectives with departmental goals. They facilitated the catchball process to ensure comprehensive input and buy-in from all levels. Key initiatives included expanding into new markets and enhancing customer service. Regular monitoring and adjustments ensured that targets were met, resulting in a 15% revenue growth and a INR 8 lacs improvement in operational efficiency over the fiscal year.
Optimizing Reaction Yields in Production
In a project within the Chemicals Industry, a company faced low reaction yields in a critical production process, leading to high raw material costs and reduced profitability. To tackle this issue, the project team performed a comprehensive analysis of the reaction parameters and implemented process optimization techniques like MLR. This included adjusting temperature and pressure conditions, optimizing catalyst usage, and integrating advanced process control systems for real-time monitoring. As a result, the reaction yield improved significantly, enhancing unit economics. The increased efficiency led to reduced raw material consumption, lower production costs, and additional revenue of INR 55 lacs annually. Overall, the project boosted profitability.
Standardizing Meeting Documentation
A project was undertaken to standardize the meeting documentation formats at the corporate office for a large MNC. There were multiple issues identified – different structures lead to confusion, missed action items and accountability, managers spending a lot of time in deciding which format to use etc. Project involved standardizing all meeting documentation formats – agenda, minutes and follow up actions etc., integrating these standardized templates within the organization mail system, training of all staff members on the new templates. The project saved approx. 250 man hours every month.
Realigning Product Design with QFD
A QFD project that focused on a new consumer electronics product (washing machine) that failed to meet key customer expectations (causing a 20% sales dip) was executed for a leading player in consumer durables. The team developed a comprehensive QFD matrix to translate customer needs (the WHAT’s) into design specifications (the HOW’s). By prioritizing features based on customer importance, they realigned the product design accordingly. This led to a 30% increase in customer satisfaction and a 15% boost in sales, generating an additional INR 5 lacs in revenue. The standardized QFD process ensured future products consistently met customer demands.
Optimizing Steel Utilization
A project was done for the construction division of a conglomerate. The construction company was involved in construction activities at multiple sites within close proximity. It faced significant wastage of steel reinforcement bars, averaging about 6% of total steel usage due to inefficient cutting practices and poor inventory management due to decentralized administration of sites. To address the issue, project team consolidated the cutting of the steel bars at one location, implemented standardized cutting plans optimized through software to minimize offcuts, introduced strict inventory controls, and coupling techniques to use the uncut pieces. As a result, steel wastage was reduced from 6% to 3%, saving approximately 250 tons of steel annually. This reduction translated into cost savings of around INR 43 lacs per year, significantly lowering material expenses and enhancing project profitability.
Optimizing Packaging Line Maintenance
A project was done in a packaged food manufacturing plant. The key issue faced was frequent machine downtimes, costing approximately INR 50 lacs annually. To address this, the project team implemented a Predictive Maintenance System using IoT sensors on critical machinery. These sensors monitored real-time performance metrics and alerted the maintenance team of potential failures. The solution included integrating IoT platforms with existing ERP systems. As a result, unplanned downtimes reduced by 40%, saving INR 30 lacs annually and enhancing overall production efficiency. Additionally, the data collected enabled better resource planning, extended machinery lifespan and uninterrupted continuous manufacturing.
We’re here for you
Are you ready to start streamlining your business with the full support of our team of experts in your field?
Across Industries
Sed ut perspiciatis unde omnis iste natus error sit voluptatem accusantium doloremque laudantium.