Your cart is currently empty!
Process Manufacturing
The process manufacturing industry produces goods by combining raw materials, supplies, or ingredients following specific formulas. This sector encompasses industries such as chemicals, pharmaceuticals, food and beverages. It relies on continuous production (24×7) processes and places a strong emphasis on quality control and regulatory compliance to ensure product consistency and safety. A significant challenge currently facing the industry is the need to adapt to increasing regulatory demands and sustainability pressures while maintaining efficiency and reducing operational costs.
Benchmark Six Sigma offers problem-solving approaches that can greatly assist organizations within this industry in enhancing quality and operational efficiency. By employing methodologies like DMAIC (Define, Measure, Analyze, Improve, Control), companies can identify and eliminate defects, streamline processes, and optimize resource utilization. Benchmark Six Sigma provides data-driven strategies and best practices, enabling organizations to reduce variability, improve product quality, and achieve higher customer satisfaction. This systematic approach promotes a culture of continuous improvement, which is crucial for staying competitive in the ever-evolving landscape of the process manufacturing industry.
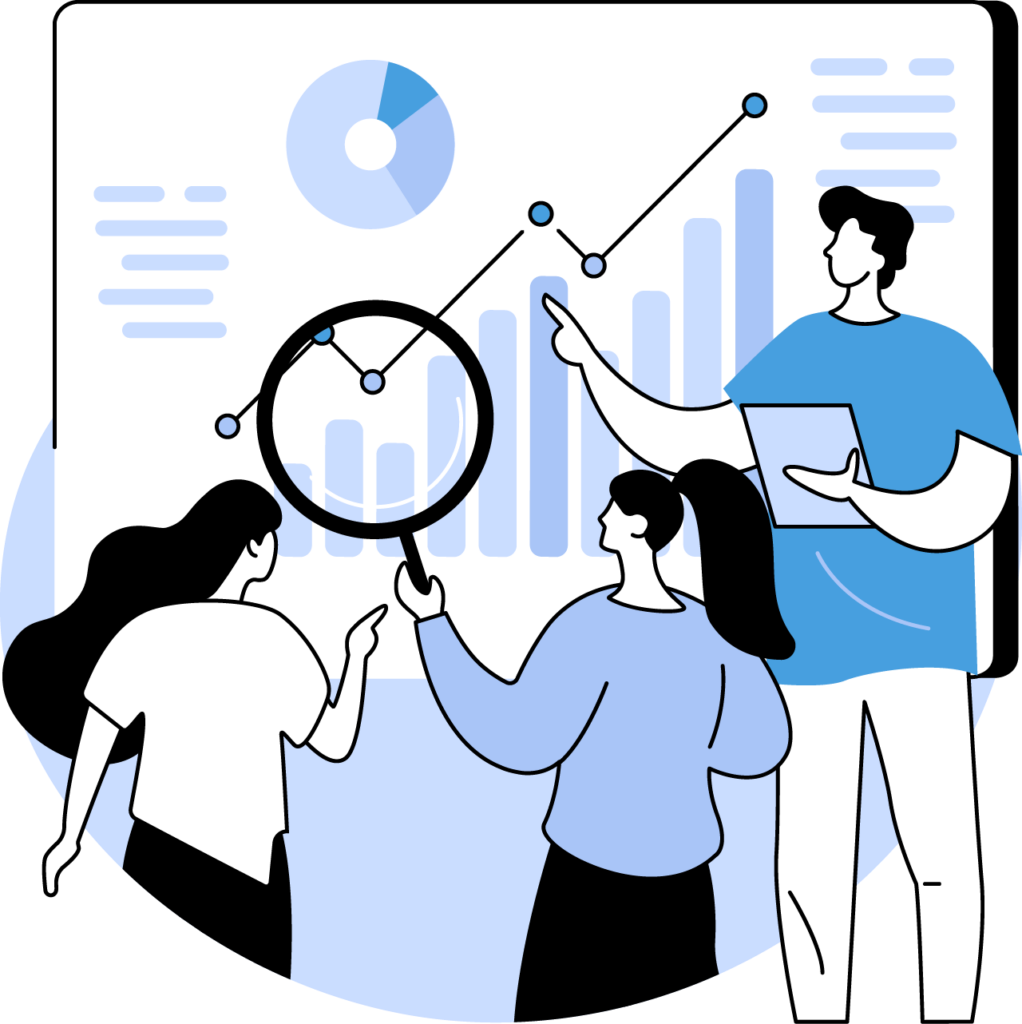
Caselets
Standardizing Meeting Documentation
A project was undertaken to standardize the meeting documentation formats at the corporate office for a large MNC. There were multiple issues identified – different structures lead to confusion, missed action items and accountability, managers spending a lot of time in deciding which format to use etc. Project involved standardizing all meeting documentation formats – agenda, minutes and follow up actions etc., integrating these standardized templates within the organization mail system, training of all staff members on the new templates. The project saved approx. 250 man hours every month.
Realigning Product Design with QFD
A QFD project that focused on a new consumer electronics product (washing machine) that failed to meet key customer expectations (causing a 20% sales dip) was executed for a leading player in consumer durables. The team developed a comprehensive QFD matrix to translate customer needs (the WHAT’s) into design specifications (the HOW’s). By prioritizing features based on customer importance, they realigned the product design accordingly. This led to a 30% increase in customer satisfaction and a 15% boost in sales, generating an additional INR 5 lacs in revenue. The standardized QFD process ensured future products consistently met customer demands.
Driving Lean Production Excellence
A Lean project was done at a renewable energy equipment manufacturer that faced inefficiencies in their production processes, resulting in delays and higher operating costs. Key issues included redundant workflows, production bottlenecks, and excessive material waste. To resolve this, the team implemented lean manufacturing principles, streamlined production lines, and introduced autonomation in critical areas. They used value stream mapping to identify and eliminate non-value-adding activities. As a result, production efficiency improved by 33%, and material waste was reduced by 21%. The company achieved annual cost savings of approximately INR 40 lacs due to increased throughput and reduced waste. These leaner processes not only lowered operating costs but also enhanced product quality and reduced delivery times.
Building Vendor Capability Metrics
A process capability model was developed for the vendor management department of an organization. The key issue identified was having no visibility on vendor performances and no way to compare their performances (as all vendors used their own capability metrics). The team used to do a monthly and quarterly review but it was more with a lag of at least a month. The vendor management team wanted a more real time monitoring of the vendor performance and also be able to compare them. A comprehensive study was conducted on all vendor processes and a robust model was built where Sigma Levels were calculated for all vendors on a weekly basis. This ensured quicker monitoring and a suitable method to compare their performance. This project was able to streamline the vendor management department and resulted in savings of INR 23 lacs by removing the low performing vendors.
Resolving Production Constraints
A project on Theory of Constraints was carried out in the packaging department. A critical bottleneck was identified that limited overall production capacity by 20%. Key solution implemented was Drum-Buffer-Rope scheduling and optimized resource allocation to address the constraint. These measures increased throughput by 25%, eliminating the bottleneck and enhancing overall system performance. The project resulted in an additional INR 18 lacs in monthly revenue and improved delivery timelines.
Cost Analysis for Procurement Savings
A project was carried out at a leading solar company to achieve a 15% reduction in procurement costs, resulting in annual savings of INR 3.5 lacs within six months by renegotiating supplier contracts. The spend data was analyzed and benchmarked against industry standards, followed by negotiations with key high-spend suppliers to secure lower prices and improved payment terms. Additionally, the project resulted in consolidation of suppliers resulting in better bargaining power in terms of volume and cost.
Ensuring Packaging Reliability
A project was done at a medical equipment company to address the surge in complaints due to packaging failures, leading to product contamination and costly recalls. The key issue identified was inconsistent sealing processes, resulting in a 20% increase in customer complaints over a year. To address this, the team conducted a thorough root cause analysis and switched to higher-quality, tamper-evident packaging. They also implemented automated sealing equipment to ensure consistency and reliability. As a result, packaging-related complaints decreased by 89%, and product recalls were reduced by 63%. Customer satisfaction scores improved significantly. The project led to annual cost savings of approximately INR 2.5 lacs due to fewer recalls and enhanced brand reputation.
Mitigating Component Failures
A project was done at an automotive component manufacturing unit. The problem was premature failures in the component. Project team used Design FMEA to identify and mitigate potential failures in the component. Initially, the component faced a 10% failure rate during testing, costing about INR 5 lacs in recalls. The team standardized FMEA processes with templates and trained a cross-functional team. They identified critical failure modes and implemented design changes, reducing the failure rate to 2%. This improvement saved the company INR 1.5 lacs in recall costs and enhanced product safety and reliability, reinforcing customer trust.
Streamlining Aerospace Product Development
A project was done for a leading aerospace company which experienced frequent delays and quality issues in new product development, leading to increased costs, potential safety risks and penalties. To address this, the project team implemented Advanced Product Quality Planning (APQP) processes, including comprehensive Failure Mode and Effects Analysis (FMEA), control plans, and process validation procedures. This initiative improved cross-departmental collaboration and standardized development protocols. As a result, product defects decreased by 27%, and time-to-market was reduced by 20%, saving approximately INR 5 crore annually in development and warranty costs. The project significantly enhanced product reliability and safety, bolstering the company’s reputation in the industry.
Optimizing Logistics Efficiency
A project was done for a leading battery manufacturer to reduce their truck detention charges by 50%. The project involved analyzing and improving loading and unloading times, implementing an appropriate scheduling system for better communications with carriers and dock assignments, reallocating resources to increase dock staffing during peak times. Collaboration with carriers was enhanced to establish better and clearer detention policies and optimize the truck arrival times. The project improved operational efficiency by reducing average detention times by 50%, increasing on-time loading and unloading rates to 95%, reduced wait time for carriers resulting in an annual saving of INR 50 lacs in detention charges.
Operations Cost Reduction Project
A cost reduction project was undertaken at a leading alumina manufacturer in their Orissa plant. Project focused on reducing the annual specific coal consumption (coal consumed per unit of alumina produced). The scope included optimizing the power plant output along with studying the leakages in the production plant. Solutions implemented included upgrades to energy-efficient motors, installation of sheds in coal storage area to prevent coal wetting, installation of variable frequency drives on pumps and fans, optimization of process parameters, implementation of waste heat recovery systems, improved insulation, and replacement of conventional lighting with LEDs. The project was able to reduce the specific coal consumption from 0.352 to 0.327 T/T leading to annual cost reduction of INR 35 Cr.
Supplier Quality Dashboard Integration
A dashboard creation project was implemented for real time monitoring of supplier QA for an FMCG company working with a large number of suppliers. The issue identified were lack of well defined KPIs for suppliers, multiple sources for data for supplier quality, no real time numbers for quick decision making. The project addressed these concerns by defining KPIs for each supplier, consolidating data from multiple sources and creating real time dashboards using Microsoft Power BI. Extensive trainings were conducted in-house and suppliers were sensitized about the new QA monitoring mechanism. This resulted in centralized tracking of supplier quality thereby releasing bandwidth of 4 resources.
Empowering Data Governance
A Data Cataloging and Metadata Management project was done for a SMSE. The organization struggled with poor data discoverability and fragmented data governance, leading to inefficiencies and compliance challenges. To address these issues, the project team implemented a robust data cataloging tool and standardized metadata management practices. They also conducted training programs for employees to ensure proper utilization and adherence to data governance policies. These solutions significantly enhanced data discoverability by 85% and established strong governance frameworks, facilitating easier data access for stakeholders and ensuring regulatory compliance.
Optimizing Boiler Performance
A Design of Experiment sub-project was done in a food chemical processing company to optimize the boiler operations. The key issue was inefficient boiler operations leading to high variations and customer rejections in the end product. Project involved conducting a 2 level factorial experiment with factors like slurry feed rate, steam temperature, steam pressure and boiler output temperature. After analyzing the design, operating settings were optimized to get a consistent rate of evaporation, SOPs were updated and staff was trained on maintaining the optimized settings. The project was able to deliver an annual benefit of INR 45 lacs.
Designing for Customer Excellence
A DFSS Green Belt project focused on a new consumer electronics product using the QFD approach. The team developed a comprehensive QFD matrix to translate customer needs (the WHAT’s) into design specifications (the HOW’s). By prioritizing features based on customer importance, they aligned the product design accordingly. This led to a quicker TAT in the design with minimal reworks. The product launch was a success as there were orders worth INR 20 lacs received within 2 days. The standardized DFSS process ensured future products consistently met customer demands.
Reducing Defects in System Design
A DFSS project was done to reduce the defect rates in the new HVAC system design. Initially, the design phase experienced a 15% defect rate, leading to increased rework costs of INR 1.2 lacs. The team implemented Design For Six Sigma methodologies and conducted a Voice of Customer (VoC) analysis. They redesigned critical components and introduced rigorous testing protocols. As a result, defect rates dropped to 5%, saving the company INR 3 lacs annually in rework and warranty costs. This project enhanced product reliability and aligned design processes with customer expectations.
Enhancing Equipment Reliability
A large tile manufacturing factory experienced frequent machine failures, leading to inconsistent production output, variation in tile quality and high repair expenses totaling about INR 5 lacs annually. To enhance reliability, a project was done to adopt Reliability-Centered Maintenance (RCM) practices. Project integrated predictive maintenance technologies, such as vibration analysis and thermal imaging, and established a routine inspection protocol. These measures identified potential failures before they occurred, reducing unplanned downtime by 40% and lowering repair costs by INR 3 lacs each year. The project also extended the lifespan of critical equipment, resulting in improved reliability.
We’re here for you
Are you ready to start streamlining your business with the full support of our team of experts in your field?
Across Industries
Sed ut perspiciatis unde omnis iste natus error sit voluptatem accusantium doloremque laudantium.