Your cart is currently empty!
Enterprise Excellence Launchpad
Building a Culture of Continuous Improvement from the Ground Up
Laborum cupidatat dolore excepteur amet enim Lorem qui aliqua aliquip laborum eu enim cupidatat. Anim id exercitation dolore incididunt qui id aute consequat eu. Non aliquip cupidatat eiusmod voluptate occaecat mollit occaecat excepteur.
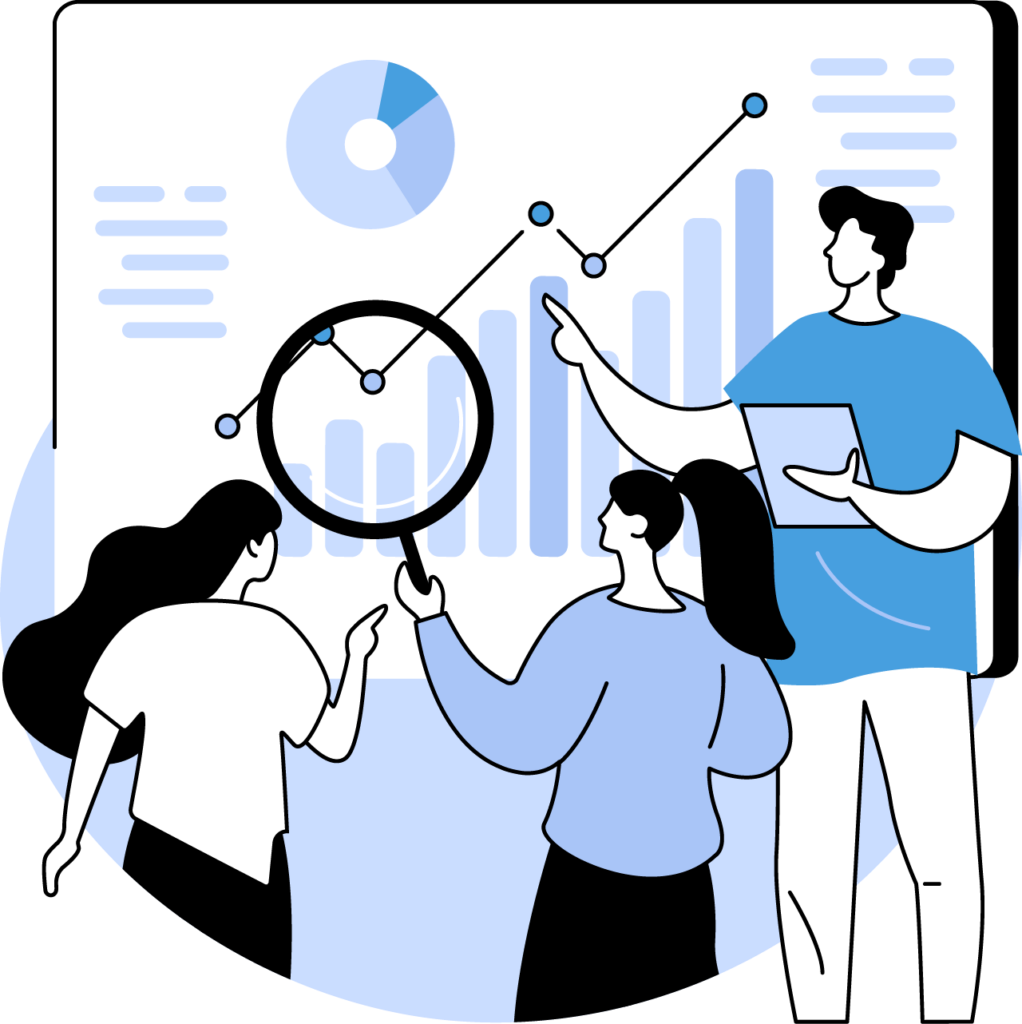
Caselets
Quality Control/ Quality Assurance > MSA
Standardizing Measurement Accuracy
A Measurement System Analysis study was conducted at a starch manufacturing company as a part of the project to reduce the variation in starch moisture content. One of the causes identified was lack of standardization in the use of the moisture meter and hence the study was performed. A crossed Gage R&R design was used in the study. Key improvements involved installing a vibration stabilizer table for the moisture meter, revision to the SOPs, training of the floor staff by the lab technician on how the sample has to be collected and spread on the dish. With the improved calibration within the team, the measurements were more accurate and correction of the measurement system reduced the range of moisture content from 4.6%-17.4% to 7.1% – 15.3%.
Business Excellence > Agile Leadership
Accelerating Product Development with Agile
The Leadership team along with Benchmark team spearheaded an Agile transformation within the product development department. They introduced Scrum methodologies, trained teams, and established iterative workflows. This shift addressed delays and miscommunications, reducing product development cycles from six months to three months. Enhanced flexibility and collaboration led to a 30% increase in project delivery speed and a INR 12 lacs boost in annual productivity.
Maintenance > Total Productive Maintenance
Integrating TPM for Workplace Efficiency
The maintenance department of a conveyor belt manufacturer struggled with cluttered workspaces, inefficient tool management, and frequent safety incidents, which hindered productivity and increased accident risks. To tackle these issues, a project was done to implement 5S methodology (Sort, Set in order, Shine, Standardize, Sustain). This involved decluttering and removing unnecessary items, organizing tools and materials systematically, establishing regular cleaning routines, standardizing maintenance procedures, conducting continuous training for staff and regular audits. As a result, tool retrieval time was reduced by 25%, saving approximately 300 man-hours annually. Additionally, workplace accidents decreased by 40%, enhancing overall safety.
Reducing Defects with Lean Six Sigma
The Master Black Belt led a Lean Six Sigma project to reduce defects in the manufacturing line. The team identified excessive waste and variability as primary issues, resulting in a 15% defect rate. By implementing standardized work procedures and waste elimination techniques, they reduced defects to 5%. This improvement enhanced product quality and increased customer satisfaction. The project saved the company approximately INR 10 lacs annually by minimizing rework and scrap costs.
Quality Control/ Quality Assurance > QMS
Implementing ISO-Based QMS
The project was done in a rubber valve manufacturing unit. The unit lacked a cohesive Quality Management System (QMS), leading to inconsistent quality standards and rejections from customers. The team developed and implemented a comprehensive QMS based on ISO 9001 standards, including documentation, standard operating procedures, and regular audits. Training sessions were conducted for all employees to ensure compliance. This integration enhanced overall quality consistency, decreased customer complaints by 40%, and increased client satisfaction, contributing to an annual INR 3 lacs revenue boost.
Driving Incremental Improvements with Kaizen
Kaizen burst activity was conducted at a call center to encourage employees to think about small incremental improvements that can make the process better and their life easier. A total of 127 ideas were collected, out of which 103 were implemented. These ideas ranged from developing a macro to combining of 3 steps in a process into a single step. Although there were no tangible benefits from this, however the activity resulted in high employee morale and improved efficiency of the processes.
Optimizing Website Maintenance and Uptime
A software maintenance project was carried out for the website of a leading trainer provider. The company experienced frequent website downtimes due to software bugs, inadequate monitoring, compromised security, addition of multiple plugins over a long period of time. These downtimes disrupted customer access to training material and affected revenue as potential customers were not able to make payments. This also lead to the team spending about 20 hours per downtime to restore the website and ensure that it is up to date. To address these issues, the project team conducted comprehensive code reviews and implemented critical bug fixes. They optimized application performance and deployed advanced monitoring tools to proactively detect potential issues. Additionally, they established a routine maintenance schedule and trained the IT staff. They also checked all installed plugins and either removed the ones no longer required or updated the required ones. These solutions successfully reduced the instances of unplanned website downtimes by 70%, ensuring higher availability and a seamless user experience. Consequently, customer satisfaction increased, and the company saw a significant boost in online transactions.
SCM/ Purchase > Strategic Sourcing
Optimizing Strategic Sourcing
A strategic sourcing project was done for a starch manufacturing company. The company had a very large supplier base for corn and it was largely convenience sourcing leading to suboptimal quality of corn resulting in operational issues and lesser yield. The project involved defining key performance indicators such as quality, delivery reliability, cost competitiveness, accessibility and responsiveness. A standardized scorecard template was created, and performance data was collected and evaluated. Suppliers were informed about the new evaluation process and collaborated in setting realistic performance targets. As a result, the company improved the raw material quality, supplier delivery reliability and were able to make more informed strategic sourcing decisions. The project also enhanced risk management by identifying underperforming suppliers early, better controlled process leading to a yield improvement of 6% and strengthened the company’s competitive position through a more efficient and responsive supply chain.
Operations > Workflow Analysis
Optimizing Water Usage for Sustainability
A sustainability improvement project was done in a beverage plant focused on Water Usage Optimization. The plant faced excessive water consumption and high utility costs, impacting sustainability efforts. To address these issues, project team implemented advanced water recycling systems and installed sensor-based monitoring to track usage in real-time. Additionally, they optimized cleaning-in-place (CIP) processes and upgraded to water-efficient machinery. These solutions enabled the reuse of up to 60% of water, significantly reducing fresh water intake. The project resulted in annual savings of INR 2.5 lacs in water and utility costs. Benefits also included enhanced sustainability through reduced environmental impact, improved compliance with water regulations, and a strengthened corporate reputation for responsible resource management. Furthermore, operational efficiency was boosted, supporting long-term profitability and environmental stewardship.
IT/ Tech > IT Infrastructure Management
Upgrading IT Infrastructure for Efficiency
A US mortgage captive unit was undertaking a big IT infra upgrade project. Benchmark project managed the whole initiative. The requirement arose when Microsoft stopped the support of the browser IE. All the legacy applications were built on IE platform and were now required to be migrated to Google Chrome along with their database connections etc. A comprehensive and cross functional assessment was done for all IT applications, their dependencies and their usage patterns. Testers were identified for each set of application. Post migration, UAT was conducted, bugs were fixed and then the applications were rolled out to the whole team. Project involved training the staff on the new applications and their revised user interfaces. The upgrade significantly improved operational efficiency and supported future growth.
Operations > Workflow Analysis
Optimizing Loan Disbursement Workflows
A workflow analysis project was done for a housing finance company in order to identify the bottlenecks in their loan disbursement process. The objective was to reduce the disbursement time from around 28 days to less than 15 days. The entire process was mapped from loan sourcing to loan disbursement, around 35 handoffs were identified in the complete process. The process was optimized to reduce the number of handoffs to 20, non-value adding steps were removed leading to increased efficiency thereby achieving the targeted TAT of 15 days.
HR/ L&D > Talent Acquisition and Retention
Reducing Employee Attrition
An attrition reduction project was done in a telecom company. The company struggled with a high attrition rate of 45%, leading to annual cost losses of approximately INR 60 lacs in recruitment and employee training. The key issues identified were employees feeling disconnected with the organization, lack of visibility on growth path, limited mobility opportunities. Key solutions included launching employee engagement programs, establishing mentorship initiatives, enhancing the benefits package, clearly defined career paths for all verticals and horizontals and deploying an AI-driven analytics tool to identify and support at-risk employees. Additionally, ESAT (Employee Satisfaction) surveys were conducted to gauge and address employee concerns proactively. As a result, attrition rates dropped to 23% within nine months, avoiding costs of INR 30 lacs and boosting ESAT scores by 25%. This project not only reduced turnover but also fostered a more satisfied and committed workforce.
Quality Control/ Quality Assurance > Sampling, Inspection and Testing
Improving Sampling Techniques for Quality
An automotive OEM was facing the problem of frequent customer complaints and rejections even when the batches were internally inspected. The issue identified was the use of convenience sampling technique leading to a biased and very small sample size. A project was undertaken to statistically determine the correct sample size and identify the best sampling technique based on the nature of the processes. SOPs were updated and staff was trained to ensure sustenance of the project. The project resulted in 70% less customer complaints and 65% less customer rejections.
SCM/ Purchase > Inventory Management
Operations > Inventory ManagementOptimizing Inventory Management
An inventory reduction project was executed at a leather products manufacturing company to reduce the cost associated with the raw material inventory. The project included studying the produce demand, variations due to seasonality, negotiations with the suppliers for time and cost, consolidation of suppliers for a tighter and integrated value chain and Just-In-Time principle. As a result of the project the raw material inventory value was reduced by 45% from INR 10,00,000 to INR 5,50,000. This initiative freed up capital, improved efficiency, and maintained customer service levels without increasing the stockouts.
Business Excellence > Hoshin Kanri
Aligning Strategy with Hoshin Kanri
Hoshin Kanri workshops are conducted along with the senior management teams where the team aligns the company’s strategic objectives with departmental goals. They facilitated the catchball process to ensure comprehensive input and buy-in from all levels. Key initiatives included expanding into new markets and enhancing customer service. Regular monitoring and adjustments ensured that targets were met, resulting in a 15% revenue growth and a INR 8 lacs improvement in operational efficiency over the fiscal year.
Operations > Capacity Planning
Optimizing Reaction Yields in Production
In a project within the Chemicals Industry, a company faced low reaction yields in a critical production process, leading to high raw material costs and reduced profitability. To tackle this issue, the project team performed a comprehensive analysis of the reaction parameters and implemented process optimization techniques like MLR. This included adjusting temperature and pressure conditions, optimizing catalyst usage, and integrating advanced process control systems for real-time monitoring. As a result, the reaction yield improved significantly, enhancing unit economics. The increased efficiency led to reduced raw material consumption, lower production costs, and additional revenue of INR 55 lacs annually. Overall, the project boosted profitability.
Implementing Sustainable Power Solutions
A project was done for a telecom infrastructure company. The company faced high operating costs due to excessive diesel consumption and frequent theft of diesel fuel at tower sites reliant on generators amid unreliable grid power. To tackle these issues, the team integrated solar panels and advanced battery storage with existing generators and installed remote monitoring systems to deter theft. This hybrid solution reduced diesel usage by 40%, from 1,000 to 600 liters per tower per month, and decreased theft incidents by 85%. As a result, the company saved approximately INR 90 lacs annually in operating costs across all towers in one circle. The project not only cut expenses and minimized environmental impact but also enhanced security at tower sites.
Quality Control/ Quality Assurance > DOE
Integrating Quality by Design
A project was done in a pharmaceuticals company which was struggling with inconsistent product quality and lengthy development times due to insufficient process understanding. To address these issues, the project team adopted the Quality by Design (QbD) approach. This involved identifying critical quality attributes (CQAs) and critical process parameters (CPPs), conducting risk assessments, and utilizing design of experiments (DoE) to optimize manufacturing processes. By integrating quality considerations from the outset, the company built robustness into the product design and manufacturing process. As a result, the company achieved improved product quality, reduced batch failures by 30%, and shortened development time by 25%. Benefits included enhanced regulatory compliance, reduced time to market and cost savings from fewer rejected batches.
Training > Business Excellence
Boosting Training Engagement
A project was done in an organization to improve the training delivery and engagement. The key issue was low completion rates hovering around 55%. The team developed an interactive e-learning platform , featuring gamified modules and mobile accessibility. This platform increased training completion rates to 80% and boosted employee engagement by 25%. Additionally, the team standardized training materials across departments, ensuring uniform skill development and reducing knowledge gaps. The enhanced training program led to a 12% improvement in overall employee performance and productivity.
Quality Control/ Quality Assurance > FMEA
Comprehensive Risk Assessment Implementation
A risk assessment project was done for a IT services provider. The company wanted to understand the risks involved in all their processes and also wanted to have a mitigation plan for them. Project involved creating detailed process maps followed by FMEA for all the processes. Basis the RPN calculated a comprehensive list of solutions were devised to systematically reduce the risks in the processes. The project resulted in a potential saving of INR 50 lacs in terms of penalties and fines.
We’re here for you
Are you ready to start streamlining your business with the full support of our team of experts in your field?